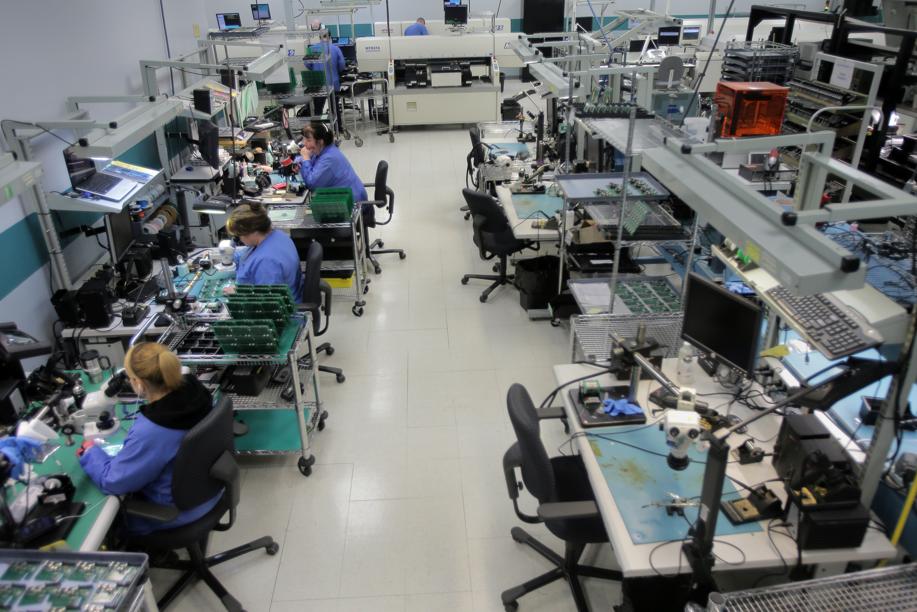
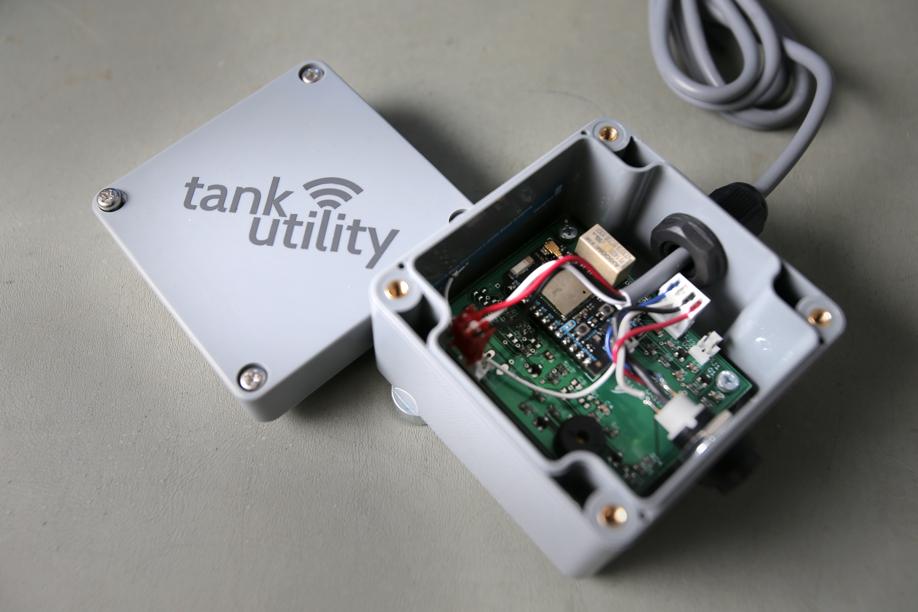
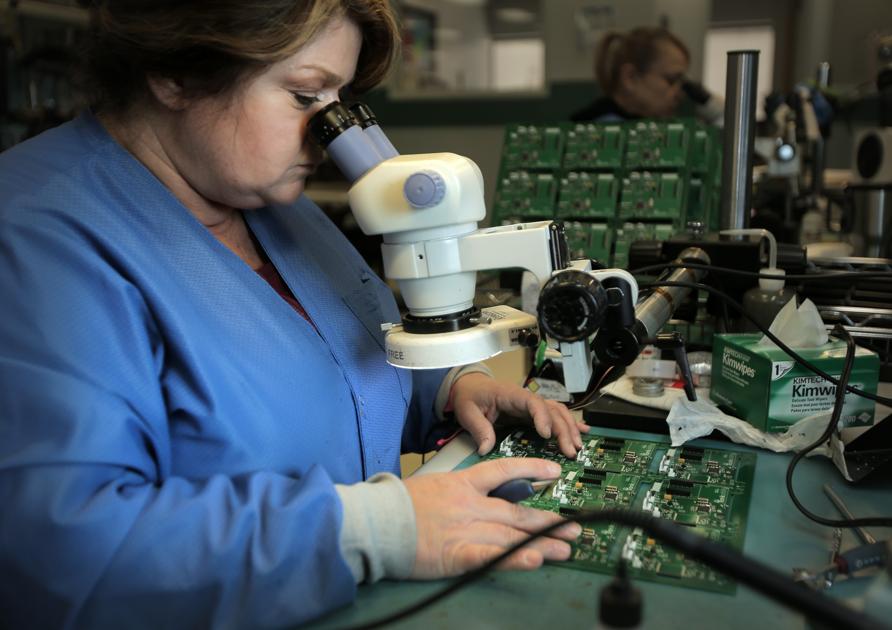
A year after he founded his Somerville startup, Nick Mashburn had a product, a smart meter that notifies fuel delivery companies when tanks need to be refilled. He also had a customer, a Canadian fuel company that wanted 1,200 meters.
What he didn’t have was someone to manufacture them.
Enter the Manufacturing Initiative, a program that connects hardware startups with manufacturers. After helping to tweak the design of his prototype, the initiative put Mashburn in touch with Lightspeed Manufacturing, a Haverhill contract manufacturer that so far has produced and shipped 500 of the smart meters for Mashburn’s company, Tank Utility.
“It was really nice to be able to find folks that could guide us through that process,’’ Mashburn said of Lightspeed, “and who had the expectation that we would be manufacturing much, much more.’’
The Manufacturing Initiative is an effort to support the state’s newest companies and one of its oldest industries, with the goal of keeping jobs and manufacturing in Massachusetts. Launched just over a year ago with a $267,500 grant from MassDevelopment, the state’s industrial development agency, the initiative is working with a group of 32 local startups and 83 Massachusetts manufacturers.
So far, that work has resulted in 14 partnerships between manufacturers and startups, including seven that have already shipped made-in-Massachusetts products.
In recent decades, US companies have turned to overseas manufacturers employing low-paid workers to undercut American factories. But hundreds of manufacturers remain in the Northeast, offering a valuable resource to startups that want closer and tighter control over the quality of their products and how they are made, according to the Manufacturing Initiative.
Manufacturers view working with a startup as an investment. The first run can be difficult, time consuming, and costly as designs are tweaked to make it easier to manufacture in volume, production lines are set up, and kinks are worked out. But if the startup takes off and places larger and larger orders, those initial costs can pay off.
For example, earlier this year the Manufacturing Initiative connected the Deerfield circuit board maker Worthington Assembly with Loci Controls, a Somerville startup that builds a system to collect methane gas from landfills. So far, Worthington has produced about 200 units for Loci, and Loci plans to order 300 more.
“You’ve got to have a long-term view of the relationships,’’ said Chris Denney, chief technology officer for Worthington Assembly, which employs 17. “You’ve got to expect that it’s going to pay off in two, three, five years even.’’
The Manufacturing Initiative is a joint venture of the Massachusetts Manufacturing Extension Partnership, a Worcester organization that supports local manufacturers, and Greentown Labs, a Somerville business incubator. With the MassDevelopment grant, the initiative hired a full-time program manager, Micaelah Morrill, the former chief of staff for state Senator Dan Wolf, a Hyannis Democrat, as well as an adviser, Peter Russo, who holds office hours to consult with hardware startups about how to find and work with manufacturers.
Morrill and Russo’s work with Tank Utility is typical of the Manufacturing Initiative's approach.
Mashburn got the idea for his smart meter after his own propane tank ran out of gas one winter. He designed a device that straps onto a fuel tank and connects wirelessly to a smartphone, and wanted to make it locally, so he could be involved with the manufacturing. He worried, though, that he didn’t have the engineering knowledge to move from a prototype, produced a few at a time, to a product that could be made by the hundreds or thousands.
Mashburn found the Manufacturing Initiative at Greentown, where Tank Utility is based.
Morrill and Russo helped Mashburn simplify the meter’s design, standardizing parts to make it easier to manufacture. Then they introduced him to a number of companies, including Lightspeed Manufacturing, which employs about 30.
Lightspeed president Rich Breault invited Mashburn to tour his Haverhill factory and made a few suggestions to optimize the design for manufacturing efficiency. The two struck a deal to produce the 1,200 units.
“If it’s a very labor-intensive product, then it’s certainly a play to go offshore,’’ said Breault, who founded the company 10 years ago.“But if you have a lower-volume product where you can automate the process, we can be very competitive.’’
Another company that has worked with the Manufacturing Initiative is Blackburn Energy, The Cambridge startup is developing a system that captures excess energy from the drive shaft of a semi truck and uses that energy to power the cabin when the truck is parked — without idling the engine. Andrew Amigo, Blackburn’s chief executive, needed a machine shop to mill a specialized part out of bearing steel.
Before Amigo found the Manufacturing Initiative, he believed he would have to go overseas to make the part to his specifications. But Morrill and Russo connected him with Atlantic Industrial Models, an industrial engineering firm a mile from his home in Essex.
“Not only did I not have to go to China,’’ Amigo said, “I could walk there from my house.’’
Jon Christian can be reached at jonathan.a.christian@gmail.com. Follow him on Twitter @jon_christian.